Understanding the Role of Injection Moulding Manufacturers in Modern Industry
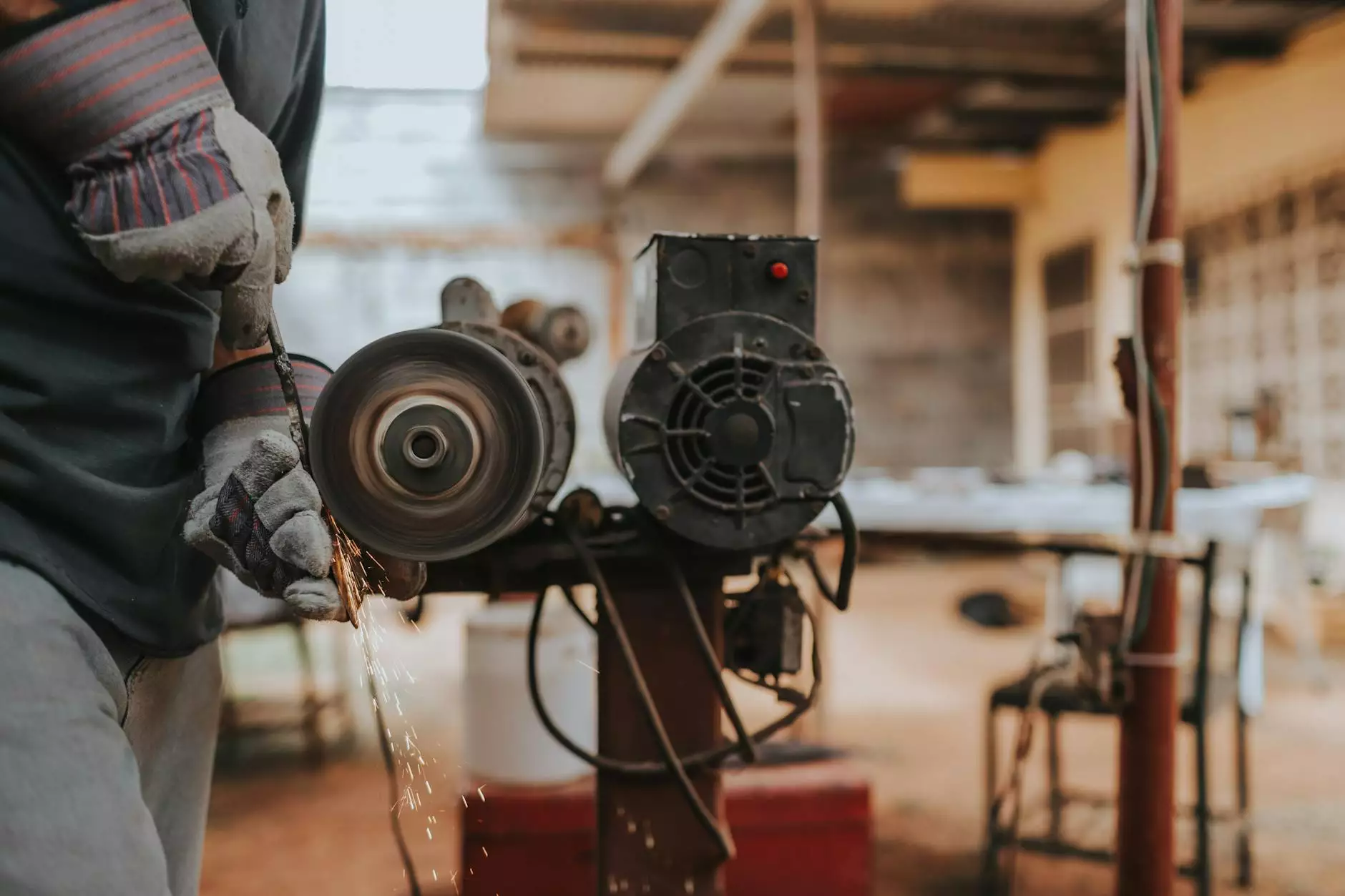
In the competitive landscape of manufacturing, injection moulding manufacturers play a crucial role in delivering high-quality products at scale. This article delves into the intricacies of injection moulding, elucidating the processes, benefits, and innovations that define this sector, particularly focusing on the capabilities of reputable manufacturers such as Deep Mould.
The Fundamentals of Injection Moulding
Injection moulding is a manufacturing process for producing parts by injecting molten material into a mould. The process is versatile and suitable for a wide array of materials, especially plastics, which are used in countless applications across various industries.
How Does Injection Moulding Work?
- Material Preparation: The process begins with the selection and preparation of the raw material. Common materials used include thermoplastics, thermosetting polymers, and elastomers.
- Heating and Injection: The selected material is heated until it becomes molten and is then injected into a pre-designed mould under high pressure.
- Cooling: Once the material fills the mould, it cools and solidifies, taking the shape of the mould cavity.
- Demoulding: After solidification, the mould opens, and the finished part is ejected.
The Benefits of Working with Injection Moulding Manufacturers
Engaging with experienced injection moulding manufacturers offers numerous advantages that can significantly enhance the production process and end product quality. Here are some key benefits:
- Cost Efficiency: High-volume production reduces per-unit costs, making it more economical compared to alternative manufacturing methods.
- Precision and Reproducibility: Advanced injection moulding techniques ensure that products are made to exact specifications consistently.
- Complex Geometries: Manufacturers can produce intricate designs that would be challenging with other techniques.
- Material Variety: The ability to choose from a range of thermoplastics and composites allows for tailored solutions for diverse applications.
Key Applications of Injection Moulding
Injection moulding is prevalent across various sectors, demonstrating its versatility. Some common applications include:
1. Automotive Industry
Injection moulding is extensively used in the automotive sector for producing high-performance components like dashboards, bumpers, and interior fittings. Manufacturers can create parts that are lightweight yet durable, which contributes to overall vehicle efficiency.
2. Consumer Goods
From toys to kitchen appliances, injection moulding is integral to the production of everyday items. Its capacity for rapid production allows manufacturers to meet market demands for consumer products efficiently.
3. Medical Devices
The medical industry relies heavily on injection moulding for producing precise parts, such as syringes, inhalers, and surgical instruments. The process facilitates high standards of sterility and functionality.
4. Electronics
Injection moulding is used to fabricate housings and internal components in electronic devices, ensuring high durability and aesthetics that appeal to consumers.
Innovations & Technological Advancements in Injection Moulding
As technology evolves, so too do the innovations within the injection moulding industry. Here are some recent advancements:
- 3D Printing in Mould Design: The integration of 3D printing technologies in creating moulds has accelerated the prototyping phase, allowing for quicker iteration and reduced time to market.
- Smart Moulding: IoT technologies provide real-time monitoring of the moulding process, enhancing efficiency and reducing waste through predictive maintenance.
- Biodegradable Plastics: The push for sustainability has led to the development of biodegradable injection moulding materials, which address environmental concerns while maintaining product performance.
- Multi-material Injection Moulding: This advancement allows for the incorporation of multiple materials in a single moulding process, enabling the production of complex components with varied properties.
Choosing the Right Injection Moulding Manufacturer
Selecting a reputable injection moulding manufacturer is vital for ensuring the success of your projects. Consider the following factors when making your choice:
1. Experience and Expertise
Look for manufacturers with a proven track record in the industry. Their experience will provide you with insights and added value in your projects.
2. Technological Capability
Evaluate the technology they use. Advanced machinery and innovative practices often lead to better quality and quicker turnaround times.
3. Quality Assurance Protocols
Ensure that the manufacturer has stringent quality control measures in place, assuring that you receive high-quality products that meet your specifications.
4. Customer Support
Strong communication and support throughout the project timeline are essential. Look for manufacturers that prioritize customer service.
Conclusion: The Future of Injection Moulding Manufacturers
The role of injection moulding manufacturers is pivotal as industries continue to evolve and adapt to new challenges. Whether it is through the adoption of innovative technologies or maintaining stringent quality standards, these manufacturers are at the forefront of producing essential products that drive our modern economy. As a business considering injection moulding services, exploring partnerships with experienced manufacturers like Deep Mould can lead to sustainable growth and success in the ever-changing marketplace.
With a commitment to excellence and an understanding of the latest market trends, injection moulding manufacturers not only contribute to the production of physical goods but also support the innovation and development of products that enhance our daily lives.